Festo EMMT-AS-60-L-LS-RMB Servo Motor
AC synchronous motor with 60mm flange size, Long length, Smooth shaft, Without shaft seal, Low voltage, standard winding, Rotatable angled plug, Absolute multi-turn encoder, and With brake. View other configurations.
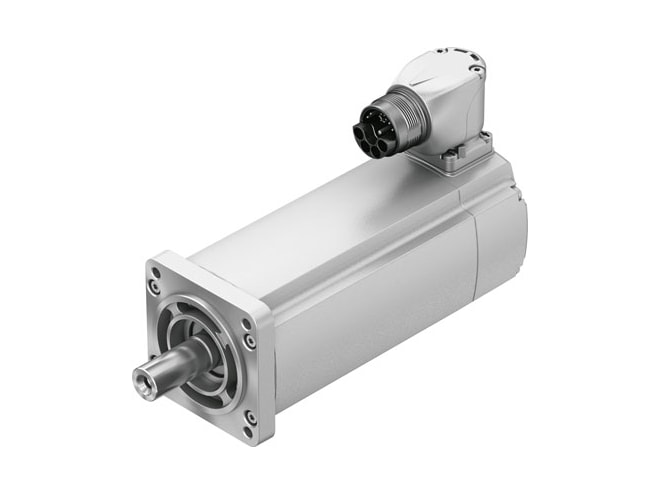
- EMMT-AS-60-L-LS-RMB
- 5242215
- EMMT-AS-60-L-LS-RMB
- By Festo
- FREE Shipping
-
Manufacturer has 19 in stock.Additional 2-3 days to process. Call for expedite options.
Overview
Features
- -15GC ambient temperature
- 40GC ambient temperature
- Up to 80°C with derating of -1.5% per degree Celsius note on ambient temperature
- 4000M max. installation height
- As of 1,000 m: only with derating of -1.0% per 100 m note on max. installation height
- 0 - 90% relative air humidity
- IEC 60034 conforms to standard
- F temperature class as per eN 60034-1
- 155GC max. winding temperature
- S1 rating class as per eN 60034-1
- Digital motor temperature transmission via EnDat® 2.2 temperature monitoring
- IM B5 motor type to eN 60034-7
- IM V1 motor type to eN 60034-7
- IM V3 motor type to eN 60034-7
- Optional mounting position
- IP40 degree of protection
- IP40 for motor shaft without rotary shaft seal note on degree of protection
- IP65 for motor shaft with rotary shaft seal note on degree of protection
- IP67 for motor housing including connection components note on degree of protection
- N concentricity, coaxiality, axial runout to dIN sPEC 42955
- G 2.5 balance quality
- <1.0% of the peak torque detent torque
- 20000H bearing lifetime under nominal conditions
- 60P interface code, motor out
- Hybrid plug electrical connection 1, connection type
- M23x1 electrical connection 1, connector system
- 15 electrical connection 1, number of connections/cores
- 995913 electrical connection 1, connection pattern
- 2 pollution degree
- RoHS-compliant note on materials
- 0 - No corrosion stress corrosion resistance class cRC
- VDMA24364 zone III lABS (PWIS) conformity
- Transport application test with severity level 2 to FN 942017-4 and EN 60068-2-6 vibration resistance
- Shock test with severity level 2 to FN 942017-5 and EN 60068-2-27 shock resistance
- RCM trademark approval
- C UL us - Recognized (OL) approval
- To EU EMC Directive cE mark (see declaration of conformity)
- To EU Low Voltage Directive cE mark (see declaration of conformity)
- In accordance with EU RoHS Directive cE mark (see declaration of conformity)
- To UK instructions for EMC cE marking (see declaration of conformity)
- To UK RoHS instructions cE marking (see declaration of conformity)
- To UK regulations for electrical equipment cE marking (see declaration of conformity)
- UL E342973 certificate issuing authority
- 325V nominal operating voltage dC
- Star inside type of winding switch
- 5 number of pole pairs
- 1.56NM standstill torque
- 1.3NM nominal torque
- 5.6NM peak torque
- 3000PMI nominal rotary speed
- 6800PMI max. rotational speed
- 16000PMI max. mechanical speed
- 410W nominal power rating of motor
- 3.5A continuous stall current
- 3A nominal motor current
- 18.3A peak current
- 0.44NMA motor constant
- 0.52NMA standstill torque constant
- 31.2YUR voltage constant, phase-to-phase
- 2.68OHM phase-phase winding resistance
- 12C14 phase-phase winding inductance
- 5C14 winding longitudinal inductivity ld (phase)
- 6C14 winding cross inductivity lq (phase)
- 3MS electric time constant
- 44MIN thermal time constant
- 1.2K/W thermal resistance
- 250 x 250 x 15 mm, steel measuring flange
- 0.49KGC total mass moment of inertia of output
- 2230G product weight
- 70N permissible axial shaft load
- 350N permissible radial shaft load
- Absolute multi-turn encoder rotor position sensor
- EQI 1131 rotor position sensor, manufacturer designation
- 4096 rotor position sensor, absolute detectable revolutions
- EnDat® 22 rotor position encoder interface
- Inductive rotor position sensor, encoder measuring principle
- 5V rotor position sensor, dC operating voltage
- 524288 rotor position sensor, position values per revolution
- 19BIT rotor position transducer resolution
- -120ARS rotor position sensor, system accuracy of angle measurement
- 120ARS rotor position sensor, system accuracy of angle measurement
- 2.5NM brake holding torque
- 24V operating voltage dC for brake
- 0.46A brake current consumption
- 11W power consumption, brake
- 52.4OHM brake coil resistance
- 700C14 brake coil inductivity
- 35MS brake separation time
- 10MS brake closing time
- 2MS dC brake response delay
- 10000PMI max. brake no-load speed
- 5600J brake max. friction work
- 0.074KGC mass moment of inertia of brake
- 10 million idle actuations (without friction work!) switching cycles holding brake
- 190 years, rotor position sensor mean time to failure (MTTF), subcomponent
- -20GC to 70GC storage temperature
- 3.6 to 14V rotor position sensor, DC operating voltage range
Documents
Accessories
Mounting Accessories
Electrical Accessories
Need Help? Call an engineer at 1-802-880-3123
We're open 8:00 am to 5:00 pm ET