Festo ERMS-32-90-ST-M-H1-PLK-AA Rotary Drive Unit
Size 32 rotary actuator unit with 90° swivel angle, PNP and IO-Link integration, and rotating plate with ball bearings. View other configurations.
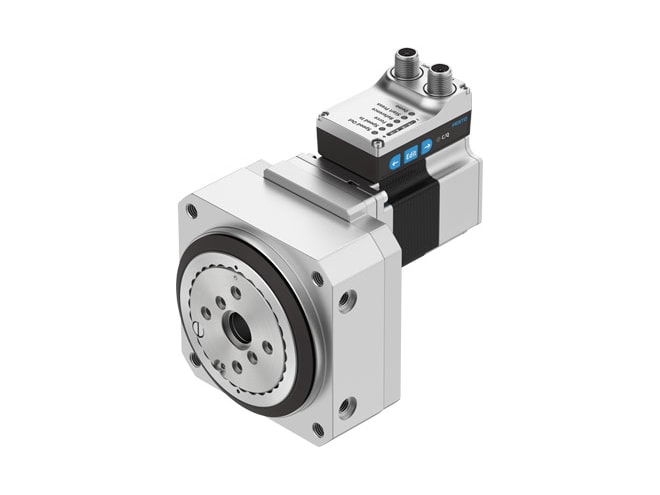
- ERMS-32-90-ST-M-H1-PLK-AA
- 8087821
- ERMS-32-90-ST-M-H1-PLK-AA
- By Festo
- FREE Shipping
Overview
Features
- 32 size
- Electromechanical rotary drive design
- With integrated drive design
- With integrated gear unit design
- Optional mounting position
- Via female thread type of mounting
- 90° rotation angle
- 7:1 gear unit ratio
- 100PMI max. rotational speed
- 100PMI max. speed at 90°
- 0.2DEG torsional backlash
- ±0.1 ° repetition accuracy
- Motor encoder position detection
- 450N max. axial force
- 550N max. radial force
- 0.0164KGY permissible mass moment of inertia
- 2304G product weight
- 1.8DEG stepper angle for complete step
- ±5% stepping angle tolerance
- 100% duty cycle
- Plugs power supply, connection type
- M12x1, T-coded according to EN 61076-2-111 power supply, connection system
- 4 power supply, number of pins/wires
- 995989 power supply, connection pattern
- Plug logic interface, connection type
- M12x1, A-coded according to EN 61076-2-101 logic interface, connection technology
- 8 logic interface, number of pins/wires
- 992264 logic interface, plug pattern
- 15 m outputs max. cable length
- 15 m inputs max. cable length
- 20 m with IO-Link® operation max. cable length
- 24V nominal voltage dC
- 5.3A nominal current
- 5A nominal motor current
- 5300A max. current consumption
- +/- 15% permissible voltage fluctuations
- 2 number of digital logic inputs
- Configurable features of logic input
- Not galvanically isolated features of logic input
- Based on IEC 61131-2, type 1 specification logic input
- 24V working range of logic input
- PNP (positive switching) switching logic for inputs
- 2 number of digital logic outputs 24 v dC
- Configurable features of digital logic outputs
- Not galvanically isolated features of digital logic outputs
- 100MA max. current digital logic outputs
- PNP (positive switching) switching logic for outputs
- Yes iO-Link, sIO-Mode support
- Device V 1.1 iO-Link, protocol version
- COM3 (230.4 kBaud) iO-Link, communication mode
- A iO-Link, port class
- 1 iO-Link, number of ports
- 2 bytes iO-Link, process data length oUT
- Move in 1 bit iO-Link, process data content oUT
- Move out 1 bit iO-Link, process data content oUT
- Quit Error 1 bit iO-Link, process data content oUT
- Move intermediate 1 bit iO-Link, process data content oUT
- 2 bytes iO-Link, process data length iN
- State In 1 bit iO-Link, process data content iN
- State Out 1 bit iO-Link, process data content iN
- State Move 1 bit iO-Link, process data content iN
- State Device 1 bit iO-Link, process data content iN
- State Intermediate 1 bit iO-Link, process data content iN
- 32-bit force iO-Link, service data iN
- 32-bit position iO-Link, service data iN
- 32-bit speed iO-Link, service data iN
- 1 ms iO-Link, min. cycle time
- 500KB iO-Link, data storage required
- Plugs iO-Link, connection technology
- IO-Link parameterisation interface
- User interface parameterisation interface
- B insulation protection class
- Stepper motor type of motor
- Absolute single-turn encoder rotor position sensor
- Magnetic rotor position sensor, encoder measuring principle
- 16BIT rotor position transducer resolution
- Positive fixed stop block referencing
- Negative fixed stop block referencing
- Temperature monitoring protective function
- User interface additional functions
- Integrated end-position sensing additional functions
- LED display
- LED ready status indication
- 997295 symbol
- 140Y26 angular acceleration
- RCM trademark approval
- KC-EMV kC mark
- To EU EMC Directive cE mark (see declaration of conformity)
- In accordance with EU RoHS Directive cE mark (see declaration of conformity)
- To UK instructions for EMC cE marking (see declaration of conformity)
- To UK RoHS instructions cE marking (see declaration of conformity)
- 5.6NM peak torque
- E8-55 interface code, basis
- IP40 degree of protection
- III protection class
- 0GC ambient temperature
- 50GC ambient temperature
- Power must be reduced by 2% per K at ambient temperatures above 30°C. note on ambient temperature
- 0 - 85% relative air humidity
- Transport application test with severity level 1 to FN 942017-4 and EN 60068-2-6 vibration resistance
- Shock test with severity level 1 to FN 942017-5 and EN 60068-2-27 shock resistance
- VDMA24364 zone III lABS (PWIS) conformity
- RoHS-compliant note on materials
- Anodised wrought aluminium alloy material flange
- Anodised wrought aluminium alloy material housing
- 2M/S speed "Speed press"
- 0.3A max. current consumption, logic
- Life-time lubrication maintenance interval
- -20GC to 60GC storage temperature
Documents
Accessories
Need Help? Call an engineer at 1-802-880-3123
We're open Mo-Th 8am to 5:30pm. Fr 8am to 5pm ET